Help:FAQ Spektrum/en: Difference between revisions
Importing a new version from external source |
Importing a new version from external source |
||
(14 intermediate revisions by 2 users not shown) | |||
Line 1: | Line 1: | ||
__TOC__ | __TOC__ | ||
<br clear="right" /> | <br clear="right" /> | ||
{{DISPLAYTITLE:FAQs and troubleshooting|noerror}} | {{DISPLAYTITLE:FAQs and troubleshooting|noerror}} | ||
==General questions== | ==General questions== | ||
===Firmware V5 for AR7210BX: Why do I have to pay for it? What benefit will I get?=== | |||
After updating your device to firmware Version 5.x.x you can do all the setup with your computer or smartphone in combination with the StudioXm App and USB2SYS/BLE2SYS interface. There is no need to do adjustments at the device using the button and the LEDs anymore (which of course is still possible to do). Additionally you can backup/restore settings, load predefined settings (currently for ALIGN TRex helicopters only), read out log data and perform a vibration analysis. As we developed the firmware and app independently from the manufacturer Horizon Hobby and did put a lot of effort in it, we charge 20 Euros for this update/upgrade plus you need the USB2SYS serial interface for the computer or BLE2SYS bluetooth interface for connection to the smartphone/tablet. In case you already have bought the PROEDITION firmware you've already paid for getting firmware from us, so you get this update for free as part of our product care. If you're not interested in the new functionality or do not want to pay anything just stay with your stock firmware V4.x.x. There is nothing wrong with it and you can still get support from Horizon Hobby.<br /> | |||
<br /> | |||
[[File:Studioxm_gallery.png|x300px|none]]<br /> | |||
<br /> | |||
===The AR7200BX that came with my Blade helicopter is not supported in StudioX=== | ===The AR7200BX that came with my Blade helicopter is not supported in StudioX=== | ||
AR7200BX with special Blade firmware on can't be programmed using StudioX as they are configured specifically for the helicopter they are installed on. Nevertheless, you can update the firmware using StudioX and make a "full" AR7200BX out of it, so that it can be used with StudioX. But note that you’ll have to use the original AR7200BX manual to setup the device in future. A factory reset will NOT revert to the Blade preset then!<br /> | AR7200BX with special Blade firmware on can't be programmed using StudioX as they are configured specifically for the helicopter they are installed on. Nevertheless, you can update the firmware using StudioX and make a "full" AR7200BX out of it, so that it can be used with StudioX. But note that you’ll have to use the original AR7200BX manual to setup the device in future. A factory reset will NOT revert to the Blade preset then!<br /> | ||
Line 129: | Line 131: | ||
===How can I increase rotation rate for aileron, elevator and rudder?=== | ===How can I increase rotation rate for aileron, elevator and rudder?=== | ||
The rotation speed of the helicopter is only determined by the length of the stick output signal. The gyros measure the actual rotation rate and the system will move the helicopter as fast as it is determined by the stick position. So simply increasing/decreasing the stick throw (mostly done by increasing/decreasing servo throw or using | The rotation speed of the helicopter is only determined by the length of the stick output signal. The gyros measure the actual rotation rate and the system will move the helicopter as fast as it is determined by the stick position. So simply increasing/decreasing the stick throw (mostly done by increasing/decreasing servo throw or using DualRate in the TX for the specified function) will increase/decrease rotation rate. Note that the rotation rate in first line has nothing to do with your cyclic pitch adjustments at Setup menu points J or L and also has nothing to do with the cyclic pitch when steering cyclic on the ground! In flight the system will automatically control the pitch as it is necessary to maintain the given rate. So always setup the cyclic pitch as mentioned in the manual and do not rely on what you see when moving the sticks on the ground. | ||
The presets at Parameter menu point B are nothing else than different preset DualRate/Expo curves inside the device. Choose the preset that fits your preferences best and that gives you a good amount of rotation rate. Using the presets (except for the "Transmitter" preset) it is recommended to not change the output signal in the TX significantly as especially when using expo this will bend, compress or stretch the curves, leading to very strange flight behavior. It just is not like adding 5% of expo as the curves between TX and AR7200BX/AR7210BX/AR7300BX will multiply and not sum together! Anyhow you may do small adjustments in stick throw, i.e. for slightly increasing the roll rate. This will not significantly deform the internal curves of AR7200BX/AR7210BX/AR7300BX. | The presets at Parameter menu point B are nothing else than different preset DualRate/Expo curves inside the device. Choose the preset that fits your preferences best and that gives you a good amount of rotation rate. Using the presets (except for the "Transmitter" preset) it is recommended to not change the output signal in the TX significantly as especially when using expo this will bend, compress or stretch the curves, leading to very strange flight behavior. It just is not like adding 5% of expo as the curves between TX and AR7200BX/AR7210BX/AR7300BX will multiply and not sum together! Anyhow you may do small adjustments in stick throw, i.e. for slightly increasing the roll rate. This will not significantly deform the internal curves of AR7200BX/AR7210BX/AR7300BX. | ||
Line 193: | Line 195: | ||
===Servos react somehow "notchy" at high frame rate. Is AR7200BX/AR7210BX/AR7300BX damaging my servos?=== | ===Servos react somehow "notchy" at high frame rate. Is AR7200BX/AR7210BX/AR7300BX damaging my servos?=== | ||
If the servos are approved by the manufacturer for the chosen update frequency, this is a normal effect. The servos get new positioning signals four times faster than if they are connected to a conventional remote control receiver. Especially servos with brushless motors run very hard and direct which causes slightly jerky movements in modes with high servo | If the servos are approved by the manufacturer for the chosen update frequency, this is a normal effect. The servos get new positioning signals four times faster than if they are connected to a conventional remote control receiver. Especially servos with brushless motors run very hard and direct which causes slightly jerky movements in modes with high servo frame rate. This is totally harmless to the servos and you will not notice in flight operation.<br /> | ||
<br /> | <br /> | ||
Line 204: | Line 206: | ||
<br /> | <br /> | ||
==RPM Governor (AR7210BX)== | |||
===RPM Governor - What is this and what does it?=== | ===RPM Governor - What is this and what does it?=== | ||
Line 242: | Line 243: | ||
===How can I get the Version 4.x.x ProEdition upgrade with AttitudeControl (Rescue bail out)? What does it cost?=== | ===How can I get the Version 4.x.x ProEdition upgrade with AttitudeControl (Rescue bail out)? What does it cost?=== | ||
To upgrade your SPEKTRUM AR7210BX you need the latest StudioX Software. This allows to connect to the freakware Network and register your device to your personal account when you connect it to the computer. Then all available updates and upgrades for the device will be displayed individually.<br /> | To upgrade your SPEKTRUM AR7210BX you need the latest StudioX Software. This allows to connect to the freakware Network and register your device to your personal account when you connect it to the computer. Then all available updates and upgrades for the device will be displayed individually.<br /> | ||
Regular device updates are free of charge. For upgrades that enable new functionality we may charge some fee. You can see the prices and buy them directly from StudioX. Available upgrades and prices also can be checked at the [[BEASTX_Devices/en|product overview page]].<br /> | |||
Please have a look [[StudioX_UpdateInstructions/en|here]] if you need further information about the update/upgrade process.<br /> | |||
<br /> | <br /> | ||
===Is AttitudeControl (Rescue bail out) also available for the SPEKTRUM AR7200BX/AR7300BX?=== | ===Is AttitudeControl (Rescue bail out) also available for the SPEKTRUM AR7200BX/AR7300BX?=== | ||
No, unfortunately this features can only be offered for AR7210BX and MICROBEAST PLUS / MICROBEAST PLUS HD. Older devices can't be used due to limitations of the hardware.<br /> | |||
<br /> | <br /> | ||
===AttitudeControl can not be activated although it is switched on at Parameter menu point | ===Parameter menu point L does not appear. After menu point K you leave the menu.=== | ||
Assign the switch channel for AttitudeControl in Function assignment menu either by moving the switch on the transmitter at menu point B or by skipping menu point B in order to use the gyro channel for the AttitudeControl. | Obviously your device doesn't seem to have the firmware with AttitudeControl feature installed. You can check this by connecting your MICORBEAST PLUS / MICROBEAST PLUS HD to the computer using the USB2SYS interface. In StudioX you can see on the device overview page which features are installed on the device. Use StudioX to upgrade to a firmware that contains AttitudeControl feature if necessary.<br /> | ||
<br /> | |||
===AttitudeControl can not be activated although it is switched on at Parameter menu point L=== | |||
Assign the switch channel for AttitudeControl in Function assignment menu either by moving the switch on the transmitter at menu point B or by skipping menu point B in order to use the gyro channel for the AttitudeControl.<br /> | |||
<br /> | |||
===Using the tail gyro gain to activate AttitudeControl, how can I control AttitudeControl and switch the tail gyro gain with flight mode switch?=== | ===Using the tail gyro gain to activate AttitudeControl, how can I control AttitudeControl and switch the tail gyro gain with flight mode switch?=== | ||
Line 287: | Line 293: | ||
===When switching on AttitudeControl on the workbench and moving the heli by hand the servos sometimes make some jerky movements=== | ===When switching on AttitudeControl on the workbench and moving the heli by hand the servos sometimes make some jerky movements=== | ||
This is absolutely normal behavior as the system doesn't simply apply full aileron, elevator or pitch input. The control input works in a much more sophisticated way. There are different curves and algorithm in the software which apply control input in a very special manner so the heli will be turned and leveled without loosing height and without moving to much around as good as possible. When turning the helicopter on the workbench this can cause some oscillations or bigger steps in servo movement (servo jumping) as the helicopter does not turn the same as it would do in reality. | This is absolutely normal behavior as the system doesn't simply apply full aileron, elevator or pitch input. The control input works in a much more sophisticated way. There are different curves and algorithm in the software which apply control input in a very special manner so the heli will be turned and leveled without loosing height and without moving to much around as good as possible. When turning the helicopter on the workbench this can cause some oscillations or bigger steps in servo movement (servo jumping) as the helicopter does not turn the same as it would do in reality.<br /> | ||
<br /> | |||
===AttitudeControl does not level my helicopter perfectly=== | ===AttitudeControl does not level my helicopter perfectly=== | ||
Line 298: | Line 305: | ||
* Please make sure your helicopter is running smooth and absolutely free of vibrations. Particularly with very small electric helis this is sometimes a difficult task, as there is not much mass to compensate for the vibrations and all electric components are placed very close to each other. If you see or hear any abnormalities like twitching tail or loud, vibrant noise it is very likely the AttitudeControl will not work as expected. You may try to place the AR7210BX unit at a different location on the heli or mount it with a different sort of gyro pad to compensate for those vibrations. Anyhow the best solution is to find the source of vibration, i.e. by removing tail and main blades and letting the motor run on the ground, and change defective/unbalanced parts.<br /> | * Please make sure your helicopter is running smooth and absolutely free of vibrations. Particularly with very small electric helis this is sometimes a difficult task, as there is not much mass to compensate for the vibrations and all electric components are placed very close to each other. If you see or hear any abnormalities like twitching tail or loud, vibrant noise it is very likely the AttitudeControl will not work as expected. You may try to place the AR7210BX unit at a different location on the heli or mount it with a different sort of gyro pad to compensate for those vibrations. Anyhow the best solution is to find the source of vibration, i.e. by removing tail and main blades and letting the motor run on the ground, and change defective/unbalanced parts.<br /> | ||
<br /> | <br /> | ||
* High temperature changes can cause the sensors to drift and in consequence cause the artificial horizon get offset. When it's very cold outside or very hot make sure the system can acclimatize when moving the helicopter from warm to cold or from cold to warm. | * High temperature changes can cause the sensors to drift and in consequence cause the artificial horizon get offset. When it's very cold outside or very hot make sure the system can acclimatize when moving the helicopter from warm to cold or from cold to warm, before powering it up and flying.<br /> | ||
<br /> | <br /> |
Revision as of 08:58, 27 February 2018
General questions
Firmware V5 for AR7210BX: Why do I have to pay for it? What benefit will I get?
After updating your device to firmware Version 5.x.x you can do all the setup with your computer or smartphone in combination with the StudioXm App and USB2SYS/BLE2SYS interface. There is no need to do adjustments at the device using the button and the LEDs anymore (which of course is still possible to do). Additionally you can backup/restore settings, load predefined settings (currently for ALIGN TRex helicopters only), read out log data and perform a vibration analysis. As we developed the firmware and app independently from the manufacturer Horizon Hobby and did put a lot of effort in it, we charge 20 Euros for this update/upgrade plus you need the USB2SYS serial interface for the computer or BLE2SYS bluetooth interface for connection to the smartphone/tablet. In case you already have bought the PROEDITION firmware you've already paid for getting firmware from us, so you get this update for free as part of our product care. If you're not interested in the new functionality or do not want to pay anything just stay with your stock firmware V4.x.x. There is nothing wrong with it and you can still get support from Horizon Hobby.
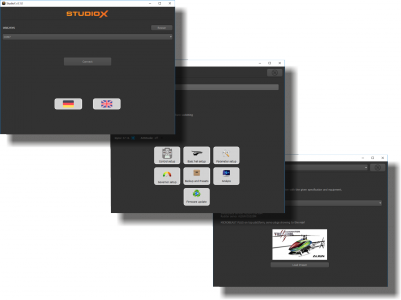
The AR7200BX that came with my Blade helicopter is not supported in StudioX
AR7200BX with special Blade firmware on can't be programmed using StudioX as they are configured specifically for the helicopter they are installed on. Nevertheless, you can update the firmware using StudioX and make a "full" AR7200BX out of it, so that it can be used with StudioX. But note that you’ll have to use the original AR7200BX manual to setup the device in future. A factory reset will NOT revert to the Blade preset then!
To keep your existing Blade settings it it important to update to firmware version 3.1.0 only, as this will not delete your setup. Once 3.1.0 is uploaded to the device, it will be recognized by StudioX and you can create restore points, change settings and more. So create a restore point of your device and then update to 4.0.14, if necessary. Updating to version 4.0.14 will reset your settings as 4.0.14 uses a new parameter set. But as you have created a restore point before, you can recover your setup and only have to setup the additional governor parameters.!
Which servos can be used with AR7200BX/AR7300BX/AR7210BX
A rule of thumb to find well suited servos for you flybarless helicopter: As strong as necessary, as fast as possible, with less dead band as available.
Servo torque in kg/cm should be at least 3-4 times the heli weight (in kilogram). Speed should be at least 0.1s/45°. The faster the better. In addition the servo should be very precise, have little gear backlash and a low dead band. And of course it should be a digital servo that supports high frame rates (200Hz or more). Also using special heli servos which are designed for maximum vibration resistance is a good choice.
Note that all the speed is useless if the torque is not enough. In doubt when two servos of a series are only slightly different in speed and torque, normally the more powerful is in advantage.
Anyhow, if in doubt ask the manufacturer of the servo if it can be used in combination with flybarless/gyro systems. Not all servos can handle the additional stress of getting different control signals every few milliseconds. Also it must be said that not all servos can be used at maximum frequency even if so it is told on the servo's data sheet. Depending on air temperature, voltage level and heli size it is possible that servos can not be driven at their limit as the servo motor or electronics may heat up too much.'
AR7200BX vs. AR7300BX
I intend to use a BEASTX flybarless system on my 600/700 heli. Should I go with the AR7300BX?
Today's servos and especially so-called high voltage servos typically have a very high power consumption. When using Futaba BLS 451 servos for example these are very modest. Savöx 1258/Align DS610 are much more demanding, one alone taking up to 15Amps peak for the instance of a second. And for very extreme example take high voltage Savöx servos SB-2271SG HV. They demand up to 27Amps (1 Servo!) peak which you can see when measure the power consumption with an oscilloscope.
So besides using a good stable and high rated power supply you have to ensure proper supply of the servos with this power. But when only connecting one servo plug with power leads into the receiver this may insufficient and cause a "bottle neck" in power flow. There is no benefit if the power supply/BEC itself can deliver 20-25A when this amount of current is not able to flow to the consumers.
So the idea behind AR7300BX is to provide a power connection that allows for using thick power cables and directly connect these to the device, so the voltage loss due to wiring and plug connection is reduced to a minimum. In general for helis with standard size servo you should always use AR7300BX, because this will eliminate the "servo plug problem" as one important factor that may be critical for your power supply.
Anyhow, it mainly depends on how you power your system. I. e. when using an ESC with only one BEC line (and if this works without issues), then there will no benefit of using the AR7300BX as you already have a "bottle neck" at the power output. The small wire will not be able to transfer more than 5 Amps continuous current. Connecting this little wire to AR7300BX's high power input will not help very much here.
If on the other hand you have at least two or even three BEC lines then this can be different as you may solder the power wires from the BEC together to a EC3 high power plug. Then you have a much lower contact resistance compared to only connect the wires using the standard servo plugs, which is a real benefit for providing a stable power supply. Ideally you have a BEC or receiver battery that already comes with thick power wires. Here it is ideal to use AR7300BX.
When using a separate receiver battery i.e. on nitro or gas helis using AR7300BX is the ideal way to connect the battery to your RC system. In addition to the adequate connection plug here you have an integrated switch system for switching the heli on and off, so there is no need to buy an extra switch.
Startup
The SPEKTRUM AR7200BX / AR7210BX / AR7300BX does not finish initialization. What can I do?
Watch the running LED lights during the init phase: If the lights A - G light up the sensor's rest positions are being calibrated, H - N show determining the RC channels and their center positions.
AR7200BX / AR7300BX: Initially the chase is from A - N. If one step is done the indication light for this step will quit running.
AR7210BX: Initially the chase is from H - N (Stick calibration). Only if this step is finished the chase from A - G (Sensor calibration) will start.
When LEDs A - G do not quit running
- The sensors register movement and calibration of rest position can not be finished. Make sure the unit/the helicopter does not get moved e.g. by wind gusts or people leaning on your work bench where the heli is standing on.
- Sensors damaged. Return the device for repair.
- Power supply voltage is dropping due to weak power supply or damaged servos.
When LEDs H - N do not quit running
- Is the transmitter switched on?
- Check whether your transmitter is correctly bound to the system.
- Keep at least 1m/3ft distance between transmitter and receiver
The brand new SPEKTRUM AR7200BX / AR7210BX / AR7300BX only shows a red flashing LED or even nothing. What's wrong?
Check very carefully whether all cables are plugged in correctly and all the plugs are connected properly at the correct position. Especially in the vertical direction check that not just 2 pins sit on the header. Also make sure that the polarity is correct on all connections. Remove all servo connections to make sure that there is no defective servo pulling too much power.
I am trying to access the menus but if I press the button after powering on the A light never goes solid or blinks. Also if I hold it for 10 seconds it doesn't appear to perform the factory reset.
To enter one of the menus you have to wait until the unit did perform the self test and did fully initialize: The Status LED must get blue or purple and the cycling LEDs A to G and H to N must have stopped.
Factory reset only can be performed when being within Setup menu. So you have at least to get to Setup menu point A (or later), release the button and then push it and keep it pushed for at least 10 seconds. Note that factory reset will only revert all parameters of parameter menu and setup menu to default. If you can't get through initialization sequence either there is a problem with the sensors or some problem with the radio signal (see topics above). Doing a factory reset won't help here anyway!
Maybe there is not enough movement or any movement at all on the rudder channel.
- Check servo throw and dual rate setting for the rudder channel in the transmitter and increase the throw.
- Is the correct stick moved? Check stick mode of transmitter and have a look at the servo monitor.
Here you can see a list of collected data: The BEASTX servo list
This list is not intended to be complete or accurate! Please ask the servos manufacturer about his recommendations regarding servo specs and usability in helicopters with flybarless systems.
- Neutral impulse: The neutral impulse normally is 1500-1520µs on any servo. Only special high speed rudder servos use a different impulse and are normally fitted to a specific gyro (i.e. Futaba gyros 760µs, Logictec gyros 960µs). AR7200BX/AR7210BX/AR7300BX supports all types of different neutral impulses for the rudder servo. On cyclic you are not able to adjust the pulse.
- Update frequency: The higher the frequency the faster the control loop will work and the more accurate the system will perform. But also the servos will be more burdened as they get more work to do and the current consumption will greatly increase.
- If using a digital servo it definitely should be capable of more than 65Hz. So if we have a unknown servo we carefully increase frame rate step by step by testing on the workbench and then fly shortly and check servo temperature very often. If there are no abnormalities like extreme heat production we again increase the frame rate and again test carefully.
This procedure can lead to damage and severe injury if not obtaining safety rules. If you want to be on the safe side go with 65Hz unless the manufacturer doesn't give you another classification. We cannot tell you the specs of a servo unless we don't have any data of this specific servo ourselves. Please ask the servos' manufacturer. We do not produce or sell any servos, we only give you the possibility to use those servos. Therefore we do not accept liability for incorrect setting.
The servo list on the website only is a collection of some servos' data. It does not say that if a servo is not on the list that you must not use it. If a servo is not on the list we simply did not test it ourselves or we could not find any data about it. Also we can't know any servo on the market. In fact the BEASTX flybarless devices are compatible to nearly any servo on the market. Anyhow, when choosing a servo for your flybarless helicopter please note this topic: Servos for flybarless usage.
I cannot get any servo horn arm to be mechanically 90° to the boom. The AR7200BX/AR7300BX does not have a tail "sub-trim" feature!? Is trimming in the transmitter allowed?
Do not trim the rudder servo by using the transmitter as this will apply a constant rotation command to the unit! When you can't get the servo horn exactly 90 degrees this has no significant effect. The "90 degrees rule" only should give some good basis for initial linkage adjustment. In flight the system will control the servo all the time anyway, so it is not an issue if the center position is slightly offset.
It is more important, that the tail servo linkage is in general adjusted correctly, so that you get asymmetric tail pitch throw: 40 degrees against main rotor torque direction, approx. 6 degrees at center position and 20 degrees in main rotor torque direction.
At Setup menu point G make sure you adjust your mechanical setup while electric trimming is active (Status LED is lit up in some color)! You mustn't do any adjustment while the system shows "reference position" (Status LED off at step G). This is only for finding the servos' true center positions (i.e. for attaching the servo arms to the servos) but is not used in any other way. If your servo arms are perfectly aligned in this position check electrical trimming anyway and readjust if necessary. Only the servo positions you see in trim mode (when the Status LED is lit up in some color at Setup step G) show the center positions that are used later onwards during setup and in operation as trimming will always be added to the servo output!
You only have to adjust one direction, whether it's left or right, it doesn't matter. Important is to exactly adjust 6° when the blades are aligned on the aileron axis as this teaches the unit the servo throw. Push the aileron stick to adjust the pitch and when the blade pitch is 6° simply push the button briefly and that's it.
When getting the 6° too early this shows that you may not use full servo resolution (not using the full throw). This can be solved by using longer blade grip linkage arms, reducing the swashplate inner diameter (shorter linkage balls) or larger swashplate outer diameter (longer linkage balls). Or simply by screwing the linkage balls on the servo horns further in (but this will reduce both cyclic and collective - the cyclic/collective ratio will not change).
Anyhow, the color is not a fixed value that is a must to reach. If you get blue you have something similar to 80% usable servo throw. The further you can go the higher the value will be. So everything from blue upwards will give a good resolution and you won't feel any disadvantages. If using good, precise high class servos, strong and with fast speed you even can fly with only red LED without any noticeable difference. Also rotorblades (flybarless blades or not) can make a difference.
On a 250 or 450 size heli you should try to get "dark blue" at exactly 6.0° as here servos normally are not so precise.
In flight
The gyro sensors do not seem to work correctly.
The rudder servo does not react or reacts very slowly to rotation of the helicopter. (The same happens to the elevator axis.)
Maybe the gain of tail gyro is too low.
- Check assignment of gain channel and adjust the gain in the transmitter as described ->here.
- Additionally when the elevator doesn't seem to work either, maybe the wrong mounting orientation has been selected. So select the correct mounting orientation in Setup menu point A.
How can I increase rotation rate for aileron, elevator and rudder?
The rotation speed of the helicopter is only determined by the length of the stick output signal. The gyros measure the actual rotation rate and the system will move the helicopter as fast as it is determined by the stick position. So simply increasing/decreasing the stick throw (mostly done by increasing/decreasing servo throw or using DualRate in the TX for the specified function) will increase/decrease rotation rate. Note that the rotation rate in first line has nothing to do with your cyclic pitch adjustments at Setup menu points J or L and also has nothing to do with the cyclic pitch when steering cyclic on the ground! In flight the system will automatically control the pitch as it is necessary to maintain the given rate. So always setup the cyclic pitch as mentioned in the manual and do not rely on what you see when moving the sticks on the ground.
The presets at Parameter menu point B are nothing else than different preset DualRate/Expo curves inside the device. Choose the preset that fits your preferences best and that gives you a good amount of rotation rate. Using the presets (except for the "Transmitter" preset) it is recommended to not change the output signal in the TX significantly as especially when using expo this will bend, compress or stretch the curves, leading to very strange flight behavior. It just is not like adding 5% of expo as the curves between TX and AR7200BX/AR7210BX/AR7300BX will multiply and not sum together! Anyhow you may do small adjustments in stick throw, i.e. for slightly increasing the roll rate. This will not significantly deform the internal curves of AR7200BX/AR7210BX/AR7300BX.
But easiest thing to do would be to switch flight behavior to preset blue (="Transmitter") and adjust the curves in your transmitter just as you like. Therefor we suggest to start with a setting of 70% D/R and 25% expo on cyclic and 85% D/R and 40% expo on tail in the transmitter and adjust the curves accordingly. When setting parameter B to "blue = TX" the internal curves will be "disabled". Here 100% stick input will give a rotation rate of apprx. 600deg/s on the rudder axis and apprx. 400deg/s for the cyclic movements (this may vary depending on TX brand as any manufacturer use another signal output as maximum, so this also can be 107, 110% or 95%).
We are often asked which percentages of expo or dual rate corresponds to the different presets. As manufacturers calculate expo curves different, we can't tell you what our preset curves correspond to which TXs expo values as we use our own expo calculation and there is no data available for comparing. We did out fly these values and programmed them in the source code so we can't tell what these are in Futaba or JR percentages. If you want to use a specific preset as your starting point we suggest to connect your AR7200BX/AR7210BX/AR7300BX to the StudioX software. Here you can see the different values for each control behavior preset and you can create a custom preset for which you may use the given values and adjust them until they perfectly fit your flying style.
Note for AR7200BX/Ar7300BX (not AR7210BX): If Parameter menu point B is set to preset "blue" and the tail gain is switched to heading lock mode you can see in operation mode by the Status LED state at which tail stick position the maximum possible rotation rate on rudder will be reached: At that specific tail stick position the Status LED will start to flash. Moving the stick to this point in flight the rotation rate of the helicopter will be as high as the gyro can control. Increasing the stick throw further the LED will go off. At this point the rate control is switched off and the rudder axis will spin uncontrolled. Here the only limit is the tail pitch throw and normally the tail will spin ultra fast. This can be used for performing tail slides or turns with very fast spinning tail. For normal flying around you should not use this as you may accidentally steer into the uncontrolled area and the tail may spin too fast or very uneven. So please check on the ground that the Status LED will not go off when giving full rudder stick deflection in your default flight modes.
The helicopter wobbles on aileron and elevator axis.
Reducing the swashplate gain does not help to suppress this effect completely.
- The helicopter's linkage ratio is not suitable for flybarless usage. In Setup menu point J adjust the cyclic pitch to exactly 6 degrees and make sure the color of the Status-LED lights up “blue”. If this is not the case change the mechanical linkage ratio of the helicopter (i.e. by moving the linkage balls further inwards on the servo horns, by mounting longer linkage balls on the swash plate outer ring or by mounting shorter linkage balls on the swash plate inner ring).
- The servo-blade combination is not good. Use faster and stronger servos and/or specific flybarless blades.
- Some linkages aren’t moving smoothly and freely. Check the mechanics for any hard points (ball linkages, blade grips). Check if the dampers are greased and that the thrust bearings in the blade grips are correctly mounted.
- Imbalance of the main rotor head. Firstly, do not tighten rotor blade bolts to much. The blades must be able to align themselves by centrifugal force. Then check blade balancing and/or try a different set of rotor blades.
The tail rotor turns around instantly when doing backwards flying.
- Tail gyro gain too low. Increase tail gyro gain as described ->here and make sure you're using the tail gyro in HeadingLock mode (using Normal-Rate mode it is nearly impossible to perform backwards maneuvers!).
- No sufficient thrust produced by the tail rotor. Check tail pitch angles. Reduce the maximum amount of available tail pitch throw at Setup menu point E to prevent the tail blades from stalling or increase the tail pitch angle if it's too small. Use different (larger) tail rotor blades or increase the rotor rpm.
The tail oscillates in horizontal position slowly and irregularly while hovering.
- The HeadingLock gain of the tail gyro is too high. Reduce the HeadingLock gain in Parameter menu point D by one step and increase the tail gain on your transmitter instead.
- Due to mechanical issues the tail gyro can not work precisely. Check the linkage and mechanics for absolute free movement without hard points and use a dedicated rudder servo that is fast and accurate and that allows a high control frequency.
During slow hovering pirouettes the helicopter is rolling out.
The pirouette optimization setting may be wrong.
- AR7200BX/AR7300BX: Adjust the pirouette optimization at Setup menu point N correctly.
- AR7210BX: Check if mounting orientation is setup correctly at Setup menu point A.
Helicopter tips over when trying to take off or tilts to one side in flight.
- Please check whether everything works properly on the ground. When giving collective pitch input the swash should move up and down properly. When giving cyclic input it should return to zero after a few seconds. This is also especially after turning on Idle up or switching between flight conditions in the transmitter. Make sure that there are no trims, mixers, etc. in any flight condition and also make sure that the sensor directions for aileron and elevator are setup correctly (Setup menu point M)!
- When taking off do not use too much cyclic input. Just let the motor come up to speed and then quickly give pitch input. Only when the helicopter is airborne the system can operate and control commands. If the helicopter sits on the ground, however, a stick input(= command to rotate the heli) would have no effect and the system would increase the cyclic pitch more and more desperately to perform a rotational movement. As soon as the helicopter will get "light" by increasing the collective pitch it will tip over abruptly. So always make sure that the swash is aligned straight during starting procedure!
- Tilting in flight: Remove the main rotor blades and let the helicopter run in all speeds on the ground (beware of the rotating parts!). Again the swash should move straight up and down when giving pitch inputs. If at a certain speed it starts to tilt in one direction and this will depend on the rotor speed then that is almost certainly a vibration problem which confuses the sensors of AR7200BX/AR7210BX/AR7300BX. Trying different adhesive pads might help (smoother or firmer mount) or installing the device in another location. But especially in the electric helicopter that brings in most cases nothing and there certainly is an error somewhere on the helicopter.
- This can be: slightly bent hub of the tail rotor, jammed or defective ball bearings, tail blades / tail rotor is not properly balanced, engine bell not balanced / comes at a certain speed to vibrate or motor bearings damaged making the motor shaft vibrate, slipped ball bearings in the torque tube tail drive system or installed in the wrong position, main gear wobbles / unbalanced; motor shaft bends and runs rough, ... actually everything that rotates on the helicopter can be the cause of such a vibration. On electric helicopter you normally should not hear, feel or see any mayor vibration (no vibrating tail fin or skids). Then it should normally be possible to attach the AR7200BX/AR7210BX/AR7300BX only with a very thin adhesive pad on electric helis. On nitro helis the situation can be slightly different as the motors do shake the more or less. This can lead to shaking of the AR7200BX/AR7210BX/AR7300BX device itself and will make the rotor pane wobble. So here trying different pads or a sandwich made of two pads and a metal plate may help to stabilize the unit better. Also the wiring can be the cause of such a shaking. But when the swash tilts as explained above the cause normally is some very high frequent (abnormal) vibration and trying around with different kinds of gyro pads only disguises the real cause and may not help 100%.
- Is the movement, however, abruptly or suddenly (similar to the twitch in a radio interference) this can especially be caused by static charges from the rear belt. Here a uniform electric potential across the entire helicopter should be done. The use of graphite spray, using a different rear belt or simply changing the belt tension can help.
- One could also consider a voltage fluctuation of the receiver power supply. It is necessary that this is stable enough, especially in terms of duration and whether the cable cross-sections and the connecting system are of sufficient size. The power supply should be dimensioned at least twice or three times as strong as expected since very high current peaks can occur in milliseconds which make the voltage sag dangerously low. In this context it may happen that the helicopter flies normally for a few minutes and then suddenly turns or rolls away in flight or even after landing the swash plate turns by itself to one direction. This is a sign that AR7200BX/AR7210BX/AR7300BX did perform a quick reboot in flight but because of the severity or duration of power failure it could not completely reload all calibration and sensor data. In this case the cause must be found and rectified and it mustn't/shouldn't be flown anymore since the receiving system was apparently close to a total failure.
Please do not confuse: A slight tilt of the swash plate when the heli is standing on the ground is absolutely normal when the so-called integrators are not fully discharged. Especially when carrying the heli or steering the sticks this can happen as the system tries to perform the necessary commands. But as the helicopter will not move as intended the system tries to keep the servo movement until the helicopter may turn. Only after approx. 30 seconds without moving the helicopter or touching the sticks, the swash will return to its normal position as the systems slowly clears its memory. The exact amount of time for this depends on the position of the thrust stick. In the middle position is the discharge at the fastest. So if possible always keep the thrust stick in center position when the heli is on the ground so that the swash plate stays leveled. Once the helicopter is airborne you will not see any of these effects as now the control loop can operate as intended. As described here to center the swashplate you can also move the cyclic stick(s) to full deflection once as this will clear integrator instantly. Only if the swash moves downright by itself to full-stop even after correcting with the sticks and only cycling power off and on resolves this problem, check that your transmitter does not send any unwanted control commands (trimming active, stick pots worn out, ...). If this is not the case please contact support as maybe there is some problem with the sensors then.
Status-LED flashes in operation mode, i.e. after landing.
The flashing Status-LED shows that a software-reset occurred during operation.
- The receiver power supply does not seem to be sufficient. The voltage during operation dropped in a critical area (<3.5 Volts). Use a stable power supply and make sure that the wiring and plugs are dimensioned big enough and feature low contact resistance. On large helicopters we recommend to use the AR7300BX with high power input.
- A reset can be triggered due to a transfer of high voltage. Take measures to prevent static discharges.
Further observations
My servos are getting warm/hot, is this normal?
Similar to a tail gyro a flybarless system is constantly working and correcting. So the servos are moving much more frequently than if they're controlled manually. Additionally to that the servos are usually driven with higher frequency to enable the system giving commands to the servos as often and quick as possible. And because of the abolition of mixing levers and the support of the auxiliary rotor plane the servos have to resist higher forces in flight.
This results to a higher power consumption and a stronger heat generation which is usually not critical. However under adverse conditions this can reach a critical range (e.g. at very high air temperatures or even if the servos are installed near other heat sources such as electric motors). In this case try reducing the driving frequency and/or the input voltage.
Servos react somehow "notchy" at high frame rate. Is AR7200BX/AR7210BX/AR7300BX damaging my servos?
If the servos are approved by the manufacturer for the chosen update frequency, this is a normal effect. The servos get new positioning signals four times faster than if they are connected to a conventional remote control receiver. Especially servos with brushless motors run very hard and direct which causes slightly jerky movements in modes with high servo frame rate. This is totally harmless to the servos and you will not notice in flight operation.
Why do the swashplate servos run very slowly when testing on the bench?
This is absolutely normal. The movement of the stick gives AR7200BX/AR7210BX/AR7300BX only a command to control the helicopter. The sticks do no longer control the servos directly. So you cannot say exactly what AR7200BX/AR7210BX/AR7300BX will do with the servos when you push one of the sticks.
I use Dual rate in my radio to decrease rotation rates but AR7200BX/AR7210BX/AR7300BX still drives my servos to full deflection when testing on the workbench.
This is absolutely normal and doesn't say anything about the rotation rates you will see in flight. Similar to the tail gyro in HeadingLock mode the system measures rotation rates and tries to maintain the rotation rate that is commanded by stick input. Now if you move the stick while the heli is standing on the ground you tell the system to rotate the heli with a certain speed. The system measures the speed and sees that nothing is happening. So it will apply more and more servo input in order to move the heli but as the heli can't move the servos will be driven to the maximum allowed deflection.
RPM Governor (AR7210BX)
RPM Governor - What is this and what does it?
Using the governor function you can simply preset your head speed with the transmitter, i.e. when you like to fly your heli with 2500rpm, you set your throttle curve in idle 1 to straight 62.5% in the TX. Then you just place your heli on the flight field, switch to Idle1 and it'll autonomously will spool up the rotor rpm to 2500rpm. Then you can take off and fly and you will get 2500rpm all over the flight, no matter what load condition the battery is or if your nitro motor will run lean. The governor will try to hold these 2500rpm as good as possible. When rotor head load increases, it'll increase throttle as necessary, when you unload the head and the head speed increases due to aerodynamic force, it'll decrease the throttle automatically. Typically this is a lot better than only controlling the motor with static curves made in the transmitter. And next time, again you will get those 2500rpm when flying the next battery/fuel tank, although this battery might be old and voltage is slightly different or the nitro motor may run more rich or lean.
For electric helicopters the governor function is a good thing if you use an ESC with bad head speed governing capability. Most (cheap) ESCs do not have a very good governor or don't feature any governor function at all. For example with some ESC you may get tail pumping at some specific rpm ranges or very abrupt throttle inputs when the load on the rotor head changes. Here you can get good results with the BEASTX governor as besides observing the motor rpm/head speed this will allow to give direct throttle input to cyclic/collective stick input. So it always will be one step ahead compared to a traditional governor function. Using a high priced ESC on the other hand, these typically have so good governor algorithms that it doesn't make any sense to use an external governor and the ESC has knowledge of what the motor is doing at the moment and what's the momentary current, voltage, etc. So here the BEASTX governor function probably will not give any performance boost.
So if you are not afraid of the additional wiring and setup procedure using the RPM governor of AR7210BX can make your heli and your ESC get a very consistent head speed governing at minimum effort. Of course if you think your ESC is working OK and that the governing is working to your satisfaction there is no need to use the governor feature.
Especially for the nitro helicopters using the governor functionality of the AR7210BX can be very handy as the unit necessary for this is already mounted to your heli. There is no need for an extra device. Just connect a rpm sensor of your choice to the unit and after performing the governor setup procedure you will not have to adjust complicated throttle curves anymore. Just choose the desired head speed you want to fly with and set it up in the transmitter, AR7210BX will do the rest including soft start and autorotation bail out feature.
Is the RPM Governor function also available for AR7200BX / AR7300BX?
For the SPEKTRUM AR7200BX / AR7300BX there is a firmware with nitro governor functionality available (Version 4.0.14) which you can get by updating with the StudioX software.
Nitro RPM Governor - When recovering from an autorotation using the autorotation bail out function the throttle increases up to nearly full throttle and stays there
Nitro helicopters react very sluggish during rpm rampup. Especially when the clutch is worn out it can take a lot of time until the rotor gains full head speed while the motor already runs at full speed, trying to spool up the rotor. This will cause the RPM Governor to stay at full speed as it detects the desired rpm seems to be faster than the helicopter allows. So you need to prevent the throttle from opening completely during spool up by decreasing the Governor quick change rate (Parameter menu point K) to a value that represents the maximum speed the helicopter is able to ramp up the throttle.
Use menu point I to change the response of the RPM Governor. This determines how fast and hard the system will open or close the throttle when the rotor rpm changes. With ideal throttle response you get a very consistent rotor head speed - the head speed should recover quickly and definite but not hectic when loading and unloading the rotor head.
- If throttle response is too low the main rotor may speed up immediately in unloaded conditions, e.g. when the helicopter is descending and the RPM Governor will only give soft throttle inputs when the head speed decreases.
- If the response is set too high on the other hand, the throttle may stutter audible when unloading the motor and/or the motor rpm will kick in very hard and overshoot after the rotor head was loaded and the rpm decreased, causing the tail rotor to turn due to the immediate load change.
The height of throttle response highly depends on factors such as heli size (blade size), motor power and performance and/or the throttle response behavior of the speed controller (when flying an electric heli). If you need to adjust the throttle response, we recommend to start with the lowest value and increase accordingly. Also you should use a lower head speed for adjustment as here you can see the effect more distinct.
Only increase the throttle response stepwise and make sure the throttle will not start to oscillate. Note that with nitro helicopters high throttle response can cause the motor to quit when the throttle is opened too fast. With electric helicopters changing the throttle very fast can cause the speed controller to overheat and especially hard changes from unloaded to loaded conditions can cause incorrect commutations of the ESC (depending on the type of motor) which can damage the ESC if this does not have appropriate protection mechanisms.
AttitudeControl
How can I get the Version 4.x.x ProEdition upgrade with AttitudeControl (Rescue bail out)? What does it cost?
To upgrade your SPEKTRUM AR7210BX you need the latest StudioX Software. This allows to connect to the freakware Network and register your device to your personal account when you connect it to the computer. Then all available updates and upgrades for the device will be displayed individually.
Regular device updates are free of charge. For upgrades that enable new functionality we may charge some fee. You can see the prices and buy them directly from StudioX. Available upgrades and prices also can be checked at the product overview page.
Please have a look here if you need further information about the update/upgrade process.
Is AttitudeControl (Rescue bail out) also available for the SPEKTRUM AR7200BX/AR7300BX?
No, unfortunately this features can only be offered for AR7210BX and MICROBEAST PLUS / MICROBEAST PLUS HD. Older devices can't be used due to limitations of the hardware.
Obviously your device doesn't seem to have the firmware with AttitudeControl feature installed. You can check this by connecting your MICORBEAST PLUS / MICROBEAST PLUS HD to the computer using the USB2SYS interface. In StudioX you can see on the device overview page which features are installed on the device. Use StudioX to upgrade to a firmware that contains AttitudeControl feature if necessary.
Assign the switch channel for AttitudeControl in Function assignment menu either by moving the switch on the transmitter at menu point B or by skipping menu point B in order to use the gyro channel for the AttitudeControl.
Using the tail gyro gain to activate AttitudeControl, how can I control AttitudeControl and switch the tail gyro gain with flight mode switch?
If applicable you may use the free programmable mixing functions of your transmitter to mix your AttitudeControl switch on the tail gyro gain output. To enable AttitudeControl you must reverse the sign of the tail gyro gain channel. So by flipping the AttitudeControl switch you must subtract or add enough channel output so that the gyro gain channel will give the amount of desired AttitudeControl gain. In the following example it is shown how this may work out on a Spektrum DX18. We use switch H to activate/deactivate AttidueControl. The AttitudeControl gain is 50% (-50% channel output in this example).
We use a mixer from switch H to the GYR channel that subtracts 100% when flipping the switch. As the gyro gain may differ between different flight modes you can create one mixer for each flight mode. Each mixer subtracts as much as necessary to get always the same amount of AttitudeControl gain (in our example -50%).
When switching on AttitudeControl on the workbench and moving the heli by hand the servos sometimes make some jerky movements
This is absolutely normal behavior as the system doesn't simply apply full aileron, elevator or pitch input. The control input works in a much more sophisticated way. There are different curves and algorithm in the software which apply control input in a very special manner so the heli will be turned and leveled without loosing height and without moving to much around as good as possible. When turning the helicopter on the workbench this can cause some oscillations or bigger steps in servo movement (servo jumping) as the helicopter does not turn the same as it would do in reality.
AttitudeControl does not level my helicopter perfectly
On the ground everything seems perfect and even the first time I switch on AttitudeControl in flight on the helis levels OK. But after some time the heli is (extremely) tilted to the side when I switch on AttitudeControl again.
The AR7210BX AttitudeControl (SAFE mode) uses gyro sensors and accelerometers to build up the artificial horizon which is necessary to determine the heli's absolute position in space. This artificial horizon is highly dependent on the sensor data input and if the sensors fail, also the artificial horizon will. The sensors can especially be influenced by vibrations which cause them to show wrong data or loose some data at all. This will cause wrong calculations and in consequence cause a wrong repositioning of the heli. The gyro sensors of AR7210BX typically are very vibration resistant and you might not see the influence of vibrations in normal flight without AttitudeControl. But as the calculation of the artificial horizon mainly is a big sum of all the sensor inputs, even the smallest influence can cause an offset of the system. Additionally the accelerometers are much more sensitive to vibrations than the gyro sensors. As these are not used in normal flight most of the time, you will not see a direct influence of vibrations on them. But for the AttitudeControl these sensors have an important role and the system can only work with limited capability if these sensors fail.
- Make sure the system is perfectly aligned to the helicopter's rotation axis. Otherwise the measurements will be incorrect by principle.
- Make sure the system is not touching the helicopter's canopy and loose wires can't hit the device in flight.
- Please make sure your helicopter is running smooth and absolutely free of vibrations. Particularly with very small electric helis this is sometimes a difficult task, as there is not much mass to compensate for the vibrations and all electric components are placed very close to each other. If you see or hear any abnormalities like twitching tail or loud, vibrant noise it is very likely the AttitudeControl will not work as expected. You may try to place the AR7210BX unit at a different location on the heli or mount it with a different sort of gyro pad to compensate for those vibrations. Anyhow the best solution is to find the source of vibration, i.e. by removing tail and main blades and letting the motor run on the ground, and change defective/unbalanced parts.
- High temperature changes can cause the sensors to drift and in consequence cause the artificial horizon get offset. When it's very cold outside or very hot make sure the system can acclimatize when moving the helicopter from warm to cold or from cold to warm, before powering it up and flying.